

Mutations in these genes induce various degrees of olfactory and reproductive dysfunction, but not the other symptoms seen in KAL-1 and KAL-2 forms of KS. The loss of function mutations in FGFR1 “fibroblast growth factor” were identified in 2003 as a cause of autosomal forms of this disease.Īn additional autosomal cause of Kallmann syndrome was recently identified by a mutation in the prokineticin receptor-2 gene (PROKR2) (KAL-3) and its ligand prokineticin 2 (PROK2) (KAL-4). It also allows migration of olfactory neurons from the olfactory bulbs to the hypothalamus. It is required to promote migration of GnRH neurons into the hypothalamus. Anosmin-1 is normally expressed in the brain, facial mesenchyme, mesonephros and metanephros. Mutations in KAL1 which encodes Anosmin-1, are responsible for the X-linked form of KS. In KS, the GnRH neurons do not migrate correctly from the olfactory placode to the hypothalamus during development and olfactory bulbs also fail to form, leading to anosmia. The presence of anosmia with micropenis in boys is suggestive of the diagnostic of KS. As a result, coated materials gain specific properties in terms of thermal insulation, solar control, reflection, etc.ģ: The primary mirror consists of 798 segments, each 1.4 metres wide but only 50 mm thick.Kallmann syndrome (KS) is a rare, heterogeneous disorder consisting of congenital hypogonadotropic hypogonadism, associated with anosmia (or hyposmia) and other clinical manifestations such as mirror movements, and renal, urological and neurosensory disorders. Patrick Van Bortel, Vice-President, New Business & Industrial Glass of AGC Glass Europe, concludes: “The selection of the proposed coater solution comes in recognition of our expertise and knowhow in building custom-designed plasma coating equipment by our teams in Gosselies, Belgium and Lauenförde, Germany.”ġ: Specialised in developing and industrialising innovative vacuum plasma coating technologies.Ģ: Magnetron sputtering is a plasma-based coating technique for depositing very thin layers of materials, including metals, onto substrate materials such as glass. AGC will do the design, manufacture, on-site assembly and commissioning of the mirror segment coating plant at the ELT Technical Facility located at Paranal Observatory in Chile. These coating operations are required by the harsh climate conditions such as sandstorms that are liable to affect the silver layers of the primary mirror. The plant will perform the initial coating and subsequent re-coating with a protected silver layer stack on the mirror segments.
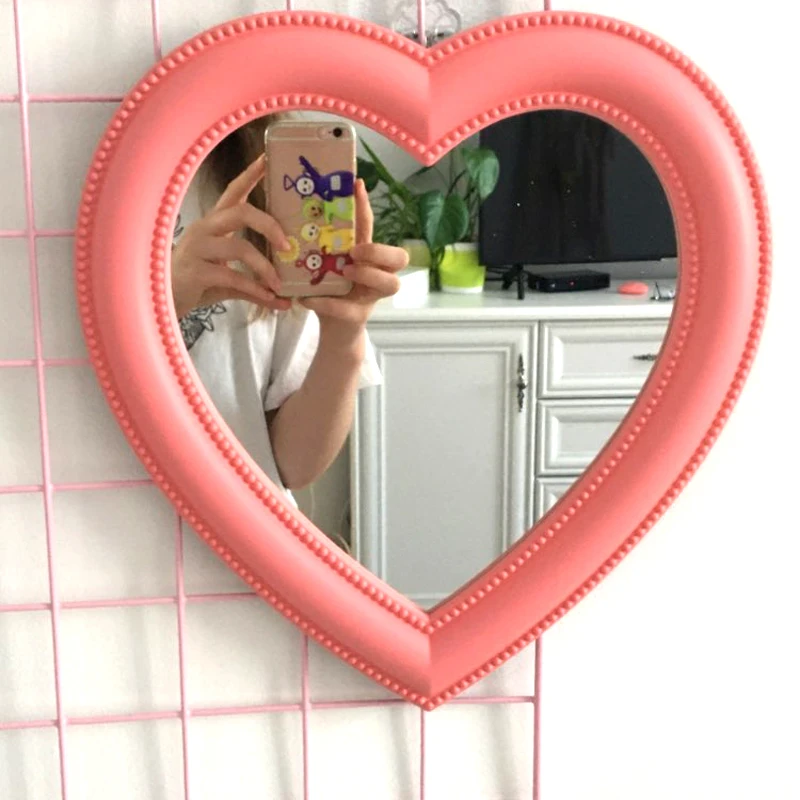
It will be equipped with a gigantic 39-meter segmented primary mirror 3 to collect the light from the cosmos and allow astronomers discover unexplored galaxies, study exoplanets and investigate other objects and phenomena across the universe. This telescope manufactured by ESO will be installed at Cerro Armazones (3,046 m) in the Atacama desert (Chilean Andes). Through its newly created unit AGC Plasma Technology Solutions 1, AGC Glass Europe has been awarded a contract by the European Southern Observatory (ESO) to supply the magnetron sputtering coating 2 plant aimed at producing the mirror for the world’s largest optical telescope, the Extremely Large Telescope (ELT).
